It's magic (almost).
Inspired by biomimicry
How do ducks and other water birds manage to not get their feathers wet? They use a thin layer fat. We use the same principle.
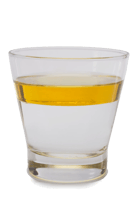
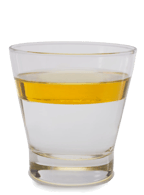


A unique approach: molecular grafting
We attach one nanometer long fatty acid molecules around cellulose fibers to obtain strong water barriers.
Unlike coating, we do not add a layer of material. Only a few milligrams of reagent are necessary per square meter, which allows us to preserve the recyclability of the initial substrate. You may not see it or feel it, but the bonds between the fibers and the fatty acids are very robust.
The treatment happens in a gas state, guaranteeing a pinhole-free result and penetrating into the thickness of the material. The full specific surface is treated, conferring outstanding durability and functionality to the material. For example, this allows to get rid of capillarity, cut or fold the substate and preserve the barriers.
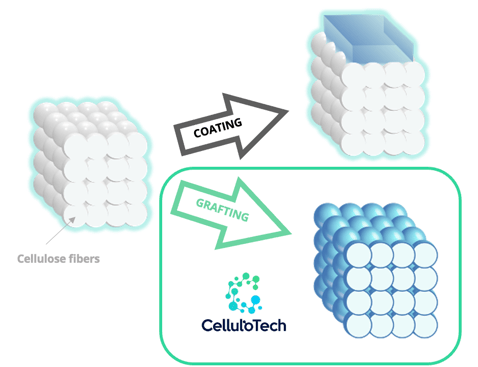
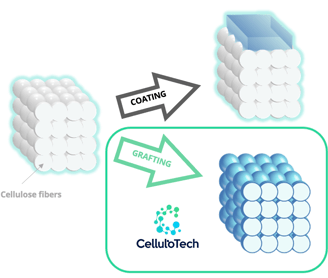
Material intensity:
up to 250x less
CO2 emissions:
up to 96% lower
Cost:
up to 91% cheaper
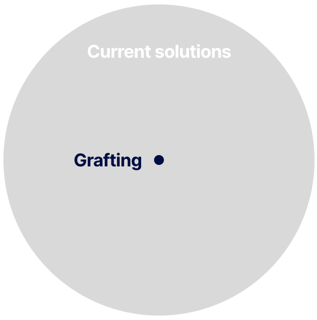
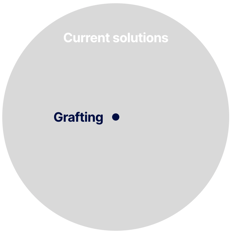
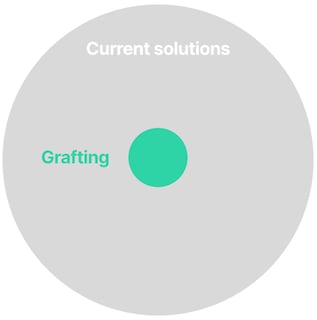
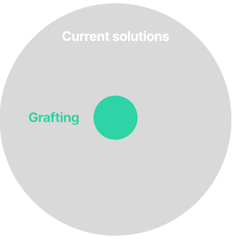
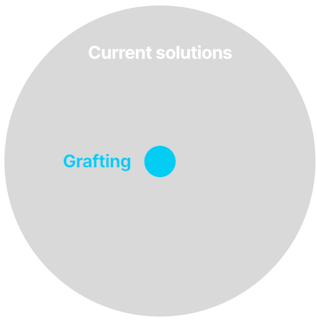
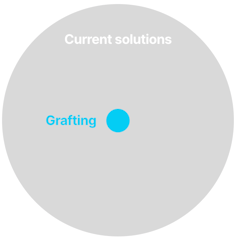
One tool, infinite possibilities
Since our technology is a chemical reaction, we can adjust many parameters (substrate, reagent, process) to achieve a wide range of possibilities.
For example, we can obtain recyclable paper with properties similar to plastic, gore-tex or silicone.
Here are some barrier values that can be achieved with different paper based substrates:
COBB600: single digit
Contact angle: up to 170 degrees
Grease Kit test: up to 12
OTR: as low as <1g per sqm per day
WVTR (standard): single digit
WVTR (humid): low double digit
Surface energy: <21 Dyne
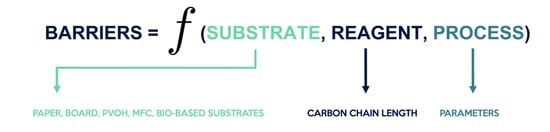
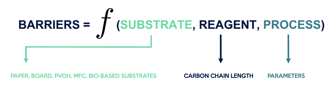
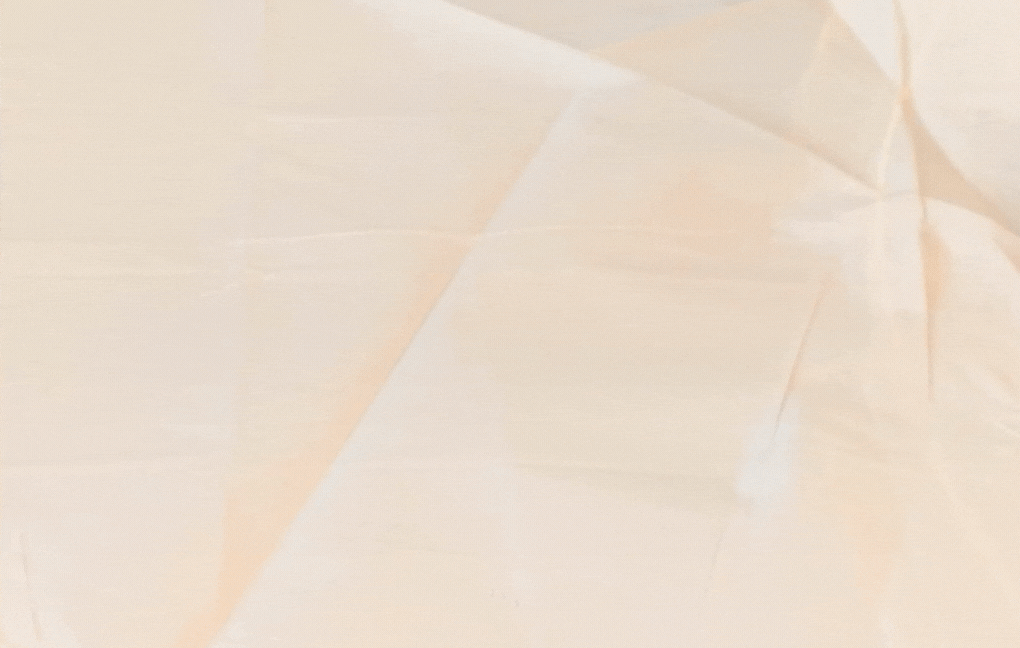
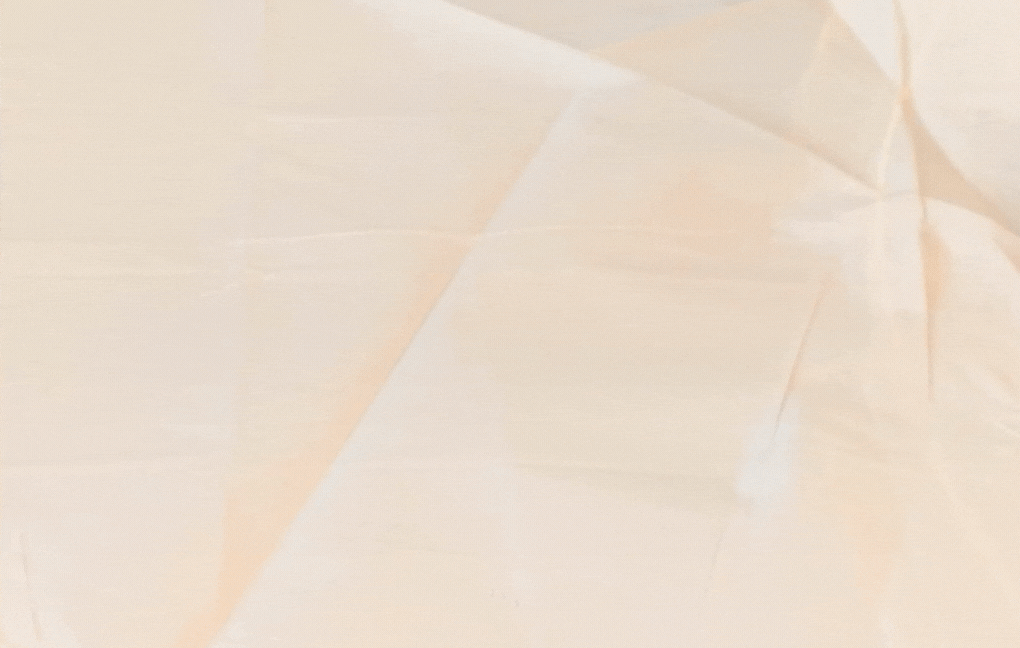
Fully bio-based
Both the substrates or the reagents we use are available at a large scale and can be harvested from the biomass.
The process is solvent-free.
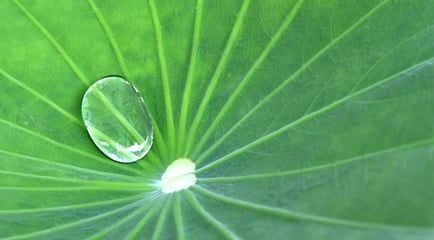
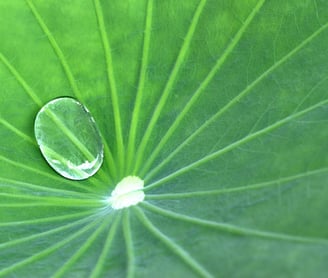
A breakthrough process
This chemistry is not completely new. Cellulotech's Chief Scientist Daniel Samain even discovered its dry and solvent-free version two decades ago. However the challenge remained to develop a scalable process for a massive industry such as packaging.
Our new proprietary process reduces the treatment time to only 0.1 second and can be adapted to 2D and 3D substrates. The equipment necessary can be adapted to online or offline processes.
Our goal? To transform cellulose and paper into the green gold of the 21st century.
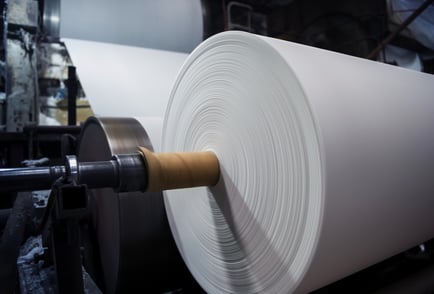
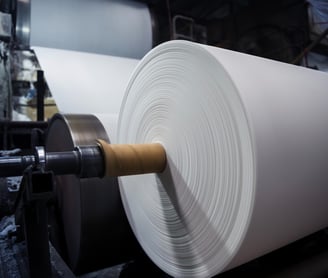
810 HUMBOLDT STREET (SUITE #A02) VICTORIA, BC, V8V 5B1 CANADA | +1 (902) 905 3076
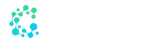
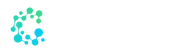